传统纺织业属于典型的高能耗、高水耗、高污染行业,尤其是纺织品染整过程中,会产生大量的废水、废渣,其中包含染料、浆料、助剂、油剂、纤维杂质和无机盐等。有机污染物含量高、碱性大、水质变化大及色度高,导致纺织业水污染处理难度大。为从源头上减少印染废水的产生,无水染色技术应运而生。
无水染色就是以有机溶剂来代替水作为介质进行染色,这意味着无需再对纱线进行前处理和染色后处理,整个印染过程完全不使用水,也无需再添加助染盐等其他化工料,就能达到甚至超过传统水介质染色的效果,印染生产中不再有废水排放。无水染色技术可实现棉线染色过程中零用水,环保非水组合介质循环利用率超99.8%,化学品耗用减少96%,染色用水减少100%,生产效率提升50%。
无水染色技术主要包括两种,一种是超临界二氧化碳染色技术,它以液态CO2作为介质,在超高压条件下使CO2液化,使染料在其中溶解,纤维在其中膨化,染料分子迅速、均匀地扩散后再减压,整个过程无须水洗,不产生废水。将其应用于实际生产,使纺织品染色效率从传统水染的8至12小时,缩短到3至4小时。另一种是用有机溶剂代替水作为介质进行染色,染色完成后,有机溶剂同样可回收循环利用。在上染过程中,节约用水100%,降低能耗39.3%,染料固色率达到97%以上,溶剂回收率达99%以上。
不久前,中国纺织工业联合会在山东青岛组织了一场项目鉴定会,多名中国工程院院士组成的专家团队给予了国际领先水平的鉴定意见。
国家先进印染技术创新中心主任毛志平告诉记者:“我们都知道中国已经是世界纺织强国,但真正的单项技术来讲,还很少有技术是中国第一个实现产业化的,无水染色技术就做到了这一点。”
生产每吨棉织物需用水约150吨,其中染色环节用水98吨,占比高达65%,耗水量最大。
青岛即发集团股份有限公司副总经理万刚说:“传统染色需要消耗大量的水资源,这既是行业的痛点,也影响了行业的发展。于是我们想能不能从这里入手,实现染色不用水。这在当时来说可以说是天方夜谭。”
针对这个难题,企业联合多家高校和科研院所,设立省级创新中心和省重点实验室,依托山东完善的工业体系和强大的制造能力,持续攻关,最终采用一种超临界二氧化碳染色技术实现无水染色。
青岛市即墨区工信局副局长黄涛说:“在中试的时候,我们即墨区的重大专项,给予了500万的资金支持,确保它的中试完成;关键的产业化阶段,省里重大工程又给予了1150万的资金扶持,每一笔资金都在最关键的时候起到了最关键的作用。”
今年上半年,首条年产1000吨无水染色产业化生产线已经正式运营,整个过程不需要一滴水,而且时间还从传统水染8至12小时缩短至3至4小时,大大提高了效率。
目前,山东列入国家绿色制造名单的项目有567个,其中绿色工厂223家,数量居全国第二位。今年,山东将加快推进废物综合利用、能量梯级利用、水资源循环利用,着力构建全链条绿色制造体系。
山东省发展和改革委员会主任孙爱军说:“紧扣绿色低碳高质量发展先行区建设这个总抓手,拿出更多新思路、新举措,对钢铁、石化、电解铝等传统优势产业‘一业一策’改造提升,推动全省经济高质量发展,奋力谱写中国式现代化山东篇章。”
文章来源: 新华网,印染学习与交流
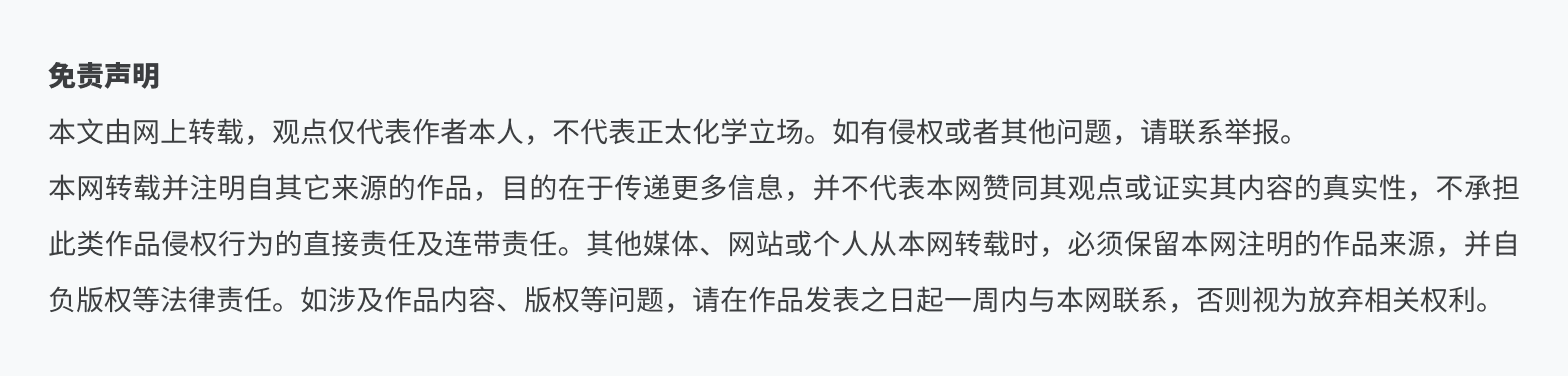