活性染料是一类新型的染料。这类染料分子中含有可以与纤维发生反应的活性基团,在染色时它能和纤维生成共价键而形成“染料一纤维”整体。
由于活性染料的分子中含有一个或一个以上的活性基团,在适当的条件下,这些活性基团能与纤维素纤维上的羟基、蛋白质纤维及聚酰胺纤维上的氨基等发生化学反应,生成共价键,所以其染色牢度很好。活性染料的分子结构大多数比较简单,故制造方便。由于在活性染料分子中含有磺酸基等水溶性基团,所以其水溶性及匀染性良好。又由于活性染料的母体大多数是酸性染料,所以其色泽很鲜艳,价格也较便宜。虽然活性染料问世时间不长,但是它已成为染色和印花中相当重要的染料。
因为活性染料分子中的活性基团容易水解。在贮存及使用的过程中,都有一定量的活性染料因其活性基团水解而失掉活性,留在染液中造成浪费。
分散剂NNO主要用于分散染料、还原燃料、活性染料、酸性染料及皮革染料中作分散剂,磨效、增溶性、分散性优良;还可用于纺织印染、可湿性农药作分散剂,造纸用分散剂,电镀添加剂,水溶性涂料、颜料分散剂、水处理剂、炭黑分散剂等。分散剂NNO在工业上主要用于还原染料悬浮体轧染,隐色酸法染色,分散性与可溶性还原染料的染色等。也可用于丝/毛交织织物染色,使丝上无上色。分散剂NNO在染料工业中主要用作分散及色淀制造时的扩散助剂、橡胶乳液稳定性,以及皮革助鞣剂。
活性染料染色过程
基本过程:
1、吸着(吸色):纤维人染液中吸取染料并向纤维内部扩散。
2、固着(固色):染料与纤维发生化学反应,生成共价键结合。
3、水洗(皂洗):未固着的染料从纤维上洗去。 染色时,活性染料首先溶解于水,染料和水分子同时进入纤维内部,并被纤维吸着。
活性染色问题
1.染料问题
主要可能出现的问题为加料时染料没有完全化开就直接加入缸中,导致出现料点,(最好是预先化好染料再加入副缸,浅色的最好在化好后过滤一次,如果直接在副缸中化料的话,一般最好用热水来化,这样可能导致部分染料水解较快,但整体来说影响不明显。最好在在保证染料完全化开后再加入染缸)另外还可以考虑是否染料本身质量的问题,这样的话要直接对来染料进行入仓前的抽查。
2.电解质问题
元明粉没有化开加入,虽然这个影响可能一般不常见,但如果元明粉没有化开(有些个别的厂家生产的元明粉杂质太多,不容易化开),如果在染色中不能完全化开的话,元明粉在染色过程中就会使布出现色斑(像这种情况最好是用温度较高的水来化元明粉,一般在副缸中先放入部分水加入元明粉后打开蒸汽来化。这样效果会好一点。)
3.碱剂问题
活性染料染色一般用纯碱作为固色剂,纯碱固色比烧碱缓慢,但其碱性是直接释放,初染率还是相对较高,这样的话在加碱的过程中开始加碱时如若控制不好就可能出现色花现象,尤其是敏感色和翠兰类大分子染料染色更容易出现色花。
4.水质问题
染色使用的水硬度太高就有可能导致染料聚集,出现色点。这需要染厂自身定期对使用的水质进行检测,如果水质硬度高的话,可以在染色过程中加入0.2-1g/L螯合分散剂来控制。螯合分散剂 不仅具有对金属离子的螯合性能,还具有分散、精练、增加白度的作用,同时还对金属离子有封锁作用,适用于前处理 、染色、后处理及其它各道工序。适应各种助剂配伍,并能有效防止硅斑浮油物或其它污染物的再附着,在染色中使用时,有一定的匀染、缓染效果。
色花原因及措施
1.煮练不匀不透造成色花
煮练不匀不透,织物上杂质去除不匀使织物部分吸湿率不一样,产生色花。
措施:
A.煮练助剂分批次定量注入,助剂要落齐。双氧水在60-70度注入效果更佳。
B.煮练保温时间一定要严格按照工艺要求保温。
C.死布缠布处理要继续保温一断时间。
2.水洗不情,布面残氧造成色花
煮练水渍不清,胚布带碱染色造成色花,煮布后布面残氧处理不干净。
措施:
A.清洗水后即10%冰醋酸中跟残碱后再洗水,使布面PH7—7.5。
B.用除氧酶助剂来完成除氧处理,正常程序定量注入冰醋酸5分钟,升温50度运行5分钟,用清水定量注入除氧酶,保温15分钟,取水样测含氧。
3.化料不均,染料溶解不充足
化料不均,染料溶解不充足造成色花。
措施:
先冷水搅拌,再用温水溶解,根据染料属性,调节化料温度,正常活性染料化料温度不宜超过60度,特殊染料要冷水化料,如艳兰br_v,可采取单独化料,一定要充足搅拌,稀释过滤后运用。
4.促染剂(元明粉或食盐)加入速度过快
后果:
过快会使绳状织物表面里带促染剂,浓度不一样,造成表里促染率不一样,而形成色花。
措施:
A.染剂应分批加入,每次加入应缓慢均匀。
B.分批加入应前次少,后次多,每次加入相隔10—15分钟,使促染均匀。
5.固色剂(碱剂)加入过快
固色剂(碱剂)加入过快,过多,造成色花。
措施:
A.正常落碱分3次定量注入,先少后多的原则,第一次用量1%10.第二次3%10.最后6%10.
B.每次加入应缓慢均匀。
C.升温速度不宜过快,绳状织物表面有差异造成吸色率相差而色花。严格要求控制升温速度(1—2℃/min)调节两边蒸气量。
6.浴比过小,造成色差色花
现在很多厂是气流缸染色设备,浴比1:4甚至1:3
措施:按工艺要求掌握水量。
7..皂洗色花
染后洗水不清,皂洗时ph含量偏高,升温过快造成色花。升温到指定温度后要保温一定时间。
措施:
洗水干净,部分厂用酸性皂洗剂中和,要在染机里运行10分钟左右,然后升温,敏感色如湖蓝,彩兰等条件方便的话,尽量测试下ph再进行皂洗。
当然随着新型皂洗剂的出现,市面有低温皂洗剂,另当别论.
8.染浴洗水不清,造成色花色斑
皂洗后残液洗水不清,从使织物表里带残色液浓度不一样,在烘干时固着在织物上形成色花。
措施:
染后要充足洗水,去除浮色。
9.加色色花
加色造成的色差(缸差,条差)色花
色差原因:
A、加料快慢程度不一样。要是促染剂量加入少,是否分次加入都有影响,如一次性加入,时间短,促染不充足,造成色花。
B、加料两边,蹭不均匀,引起条差,如一边深色多,少的一边浅。
C、保温时间
D、剪样对色手法不一样造成色差。
要求:同一手法剪样对色。
如:保温20后剪样对色,且剪样后水洗程度不一样。
E、浴比大小不一造成色差。小浴比:色深 大浴比:色浅
F、后处理程度不一样。后处理充足,浮色去除充足,较后处理不充足的要色浅。
G、两边,中间有温差,造成条差
加色要慢,至少定量注入20分钟,敏感色在30-40分钟。
加料追色
1)色浅状况:
A、首先要核对原工艺处方单,根据色差程度跟织物重量称取染料。
B、追色染料必须充足溶解,充足稀释,并经过滤后运用。
C、追色对应在常温条件下加料,加料对应缓慢,均匀,以防操作过急造成再色花。
2)色深状况
A、加强皂洗,充足后处理。
B、加Na2CO3作轻微脱色处理。
掌握正确方法,才能有效避免质量问题的发生,需要染色一线的不断学习和摸索,对色师傅尽力加好色,为染厂创造更大利润。
文章来源: 笙以金,染化严选
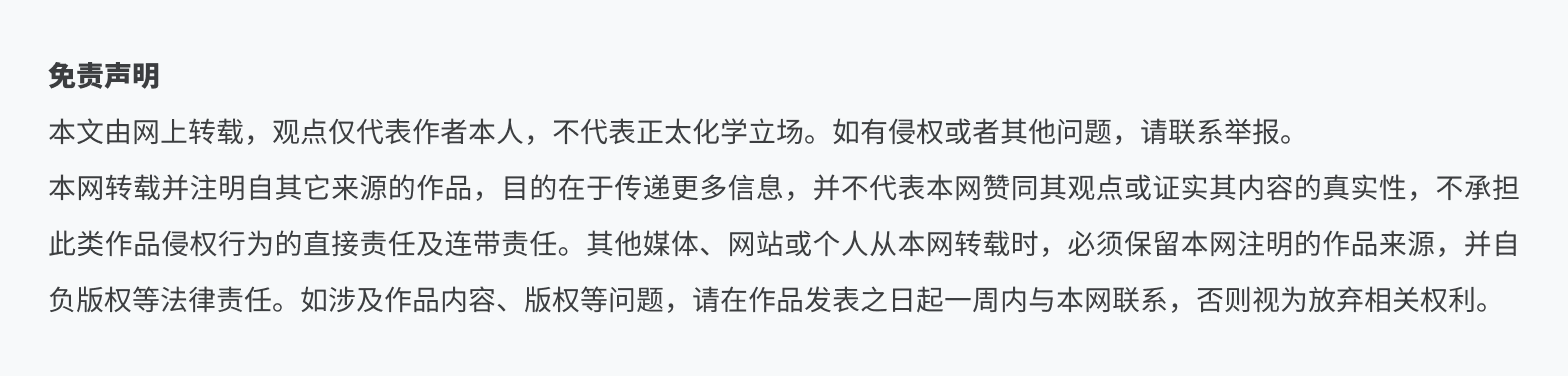